The Laser Cleaning Process
The laser radiation cleaning process has become a solid alternative to the more raditional methods of thermal, mechanical, and chemical nature in a wide range of materials and applications, such as removal of polymeric coatings, cleaning of artworks, antiquities, and buildings; nuclear and biological decontamination; mold cleaning; and particle removal in the microelectronics and optics industries.
The advantages over current technologies include, in addition to those typically applicable to all laserprocesses (precision, flexibility, ease of automation), two main important aspects. One of the misthesustainability of the process from an environmental pointofview, due to the fact that the use of potentially toxic and polluting organic solvents, such as those used in techniques based on chemical removal, is eliminated.
On the other hand, there is the fact that lasers offer the possibility of dealing with new problems, unapproachable by alternative methods.
Metal surfaces are particularly suitable for many laser cleaning and stripping applications. Coatings, residues, or oxides to be removed are affected while the laser ablation stops at the substrate due to reflection on the metal surface. The power density of the laser beam can be easily adjusted to achieve the desired result. This is an important advantage compared to other conventional methods.
In addition, vaporized materials can be captured in the same zone of their emission through a smoke extraction system, eliminating the possibility of contaminant emissions in the work area and the need for a subsequent cleaning stage.
As for the nature of the laser, the vast majority of cleaning lasers employed pulsed sources with nano second regimes. Longer pulses than nano second pulses induce deeper thermal effects on the substrate, and the risk of damaging the material is therefore greater. Shorter pulses than nano second pulses, like femtosecond pulses, may work in some cases, although, due to their reduced average power, they are not very suitable for industrial use.
Continue Wave Laser Versus Pulsed laser for laser cleaning
The characteristics of the different type of lasers involve different types of removal mechanisms.
-
The Continiuos Wave laser is a fiber laser in continuous mode and the cleaning mechanism is basically carbonization, photothermal, or pyrolytic.
-
The Pulsed Wave laser, MOPA or Q-Switched, is a fiber laser that operatesin a nano-seconds pulse regime and the cleaning mechanism a photomechanical ablation phenomenon.
The pulsed mode lasers is used to remove epoxy paint contamination on metallic surfaces, to clean contaminants from optical glasses , to remove impurities from steel sheets, to remove titanium nitride from hardmetal or carbonsteel, to clean stones and historical heritage pieces, and to remove graffiti, among other uses. These are usually laser sources of power between 1 and 300W and with fluences of 10J/cm2 or less. This type of equipment is usually selected for delicate operations and thin layers.
The continuous mode fiber laser is used to remove air-drying enamels, for the removal of silicone rubber (by applying black paint to improve absorbance), and for stripping polyester paint on an aluminum substrate.
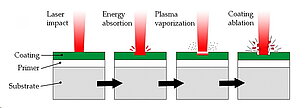
Photomechanical Effect
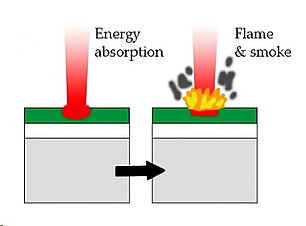
Photothermal effect
The removal of particles and the removal of solid surface layers.
Two clearly differentiated fields have been developed under the umbrella laser cleaning: the removal of particles and the removal of solid surface layers.
In the frame work of this second category, other processes of laser stripping or separation could also be included if not only the removal of contaminant layers is considered, but also other related processes, such as degreasing, removal of oxides, or stripping of paint and polymeric coatings.