New Way of Paint Removal - Laser Cleaning
If you would like to remove delicately surface painting layers and do not want any damage to the base material, fiber laser cleaning machine would be the perfect choice. Laser cleaning can be applied to remove paint from various materials including metals, composites, plastic, rubber and stones. Coatings such as paint, varnish and rust can be cleaned with ease. Laser paint removal, to be sure can help update and reuse the material with paint you no longer needed.
The traditional methods for paint removal involves the use of chemical reagent or abrasive media blasting. These methods are quite time consuming, leaving damage on the base material and cause extra costs such as purchasing and safe disposal of the chemical solvents. These issues bring us a better solution - laser cleaning equipment! How do we use it for paint removal? To understand this, we must first understand the cleaning mechanism of laser cleaning equipment.
The cleaning process of laser cleaning equipment depends on the light pulse generated by the laser, which is based on the optical physical reaction caused by the interaction between the high intensity beam, the short pulse laser and the polluted layer. Laser cleaning equipment plays a crucial role in many industries, such as automobile manufacturing, semiconductor wafer cleaning, precision parts processing and manufacturing, building external wall cleaning, protection of cultural relics, circuit board cleaning, precision parts processing and manufacturing and LCD cleaning. For example, laser cleaning systems have long been used in the aviation industry. The surfaces of the aircraft have to be repainted after a certain period of time, but the old paint has to be completely removed before the repaint. The traditional mechanical paint removal method would do damage to the metal surface of aircraft, which brings hidden danger to the safety of flight. With multiple laser cleaning equipment working simultaneously, the paint layer can be completely removed from the surface of an A320 Airplane in two days without damaging the metal surface.
The paint applied to the surface of the metal acts as a special layer to protect the metal from corrosion and oxidation. In order to carry out effective cleaning on the premise of ensuring the safety of the substrate material, the laser parameters must be adjusted according to the situation so that the energy density of the light pulse is strictly controlled.
Each laser pulse removes a layer of pollution of a certain thickness. If the fouling layer is thick, multiple pulses are required for cleaning. The number of pulses required to clean the surface depends on the degree of surface contamination. An important result of the two thresholds is the self-control of cleaning. Light pulses whose energy density is higher than the first threshold will remove contaminants until they reach the substrate. However, because its energy density is below the destruction threshold of the substrate material, the substrate is not damaged.
Based on the above theories, when the laser cleaning equipment is used for paint removal on the metal surface, the threshold value should be controlled appropriately. To achieve good quality, laser paint removal needs 2-3 steps. Firstly, a main pass using long pulse duration and high pulse energy removes the majority of the paint layer. For the second pass, the remaining paint coating can be removed by short pulses and high scanning speeds without damaging the substrate. If necessary, second pass can always be repeated. Finally an optional third pass to improve surface quality.
SELECTIVE LASER COATING REMOVAL AND LASER PAINT STRIPPING
The laser enables selective paint stripping
In many industries surfaces are being coated with cathodic dip (CDC) or powder coatings. Such paints provide the durability and anti-corrosion properties needed in manufacturing of cars or other surfaces facing outdoor climate.
However, certain areas of such parts need to be free of any coating to assure good welding or adhesion behavior, tight mechanical fit or a blank metal surface for electrical connections.
A common process to avoid coatings on these bond interfaces is to mask such areas before coating and remove the masking afterwards. This is a tremendous waste of resources, difficult to automate and environmentally questionable.
The use of laser paint stripping systems allows to coat the parts without masking and selectively remove the coatings on the bonding interfaces in a subsequent process.
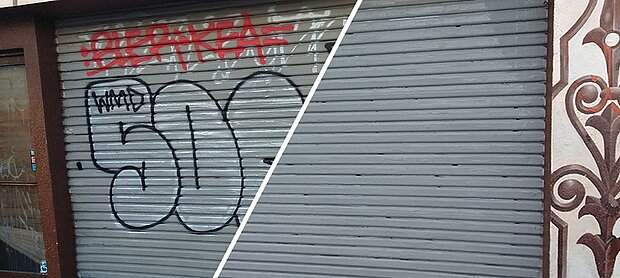
Laser SWIPE Cleaning systems can remove coatings partially in layers, precisely in discrete areas as well as completely. Laser de-coating uses pulsed and scanned beam of laser light for a process that’s free of liquids, abrasives and chemicals used with traditional methods. Paint removal technology that’s green and clean.
-
Powerful laser systems for high de-coating rates
-
No damage to substrates
-
One-step, gentle, precise & residue-free
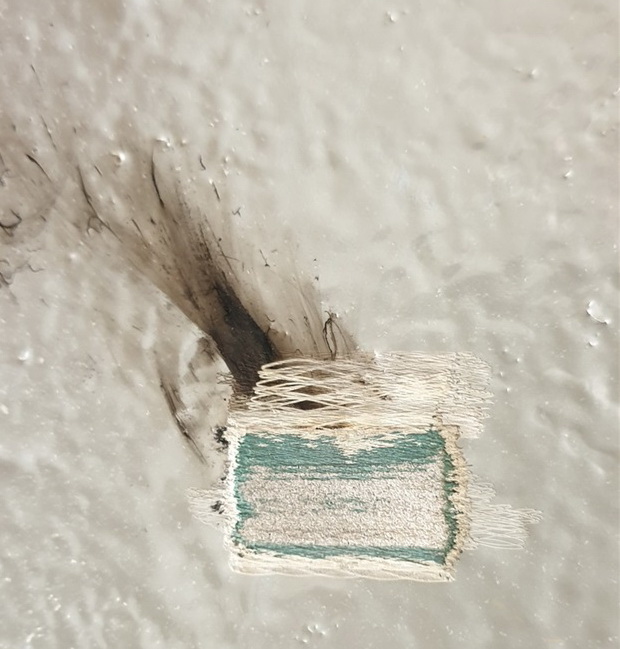
Pierce through the layers of newer paint.
If you find a part with places that have new paint applied over the original, then sand-blasting and chemical washes put that paint at risk. That forced action you to need to make is a hard decision: do you risk sacrificing part of the original color to fully remove the new layers, or do you leave it as it is?
But with laser cleaning, you can get the surface cleared away layer by layer. We can remove that newer paint without touching the original material. Laser cleaning can be adjusted to remove minuscule layers of material at a time, so a first pass removes the bulk of the unwanted paint, a second time focuses on scanning and spot removing, and following passes ensure complete removal.
Indicational Surface Cleaning capacity for each laser power
This are only indicational values for Reference, based on our own experience, each case must be checked specific and results depend on the layers and the underground
Surface cleaning indicational capacity | layer thickness | 100Watt | 200Watt | 300Watt | 500 Watt |
---|---|---|---|---|---|
Paint | m²/h | m²/h | m²/h | m²/h | m²/h |
<50µm | 1 | 2 | 2,5 | 5 | |
<100µm | 0,5 | 1 | 1,2 | 3,0 | |
>100µm | 0,2 | 0,5 | 0,8 | 1,4 | |
Oxide Layer or coated surface | m²/h | m²/h | m²/h | m²/h | m²/h |
<25µm | 5 | 9 | 12 | 15 | |
<50µm | 2,5 | 4,5 | 6 | 7,5 | |
>50µm | 1,5 | 3 | 4 | 5 |